Abrasive Water Jet Cutting Process and Benefits
Abrasive water jet cutting is a high-precision, cold-cutting process that uses a mixture of high-pressure water and abrasive particles to cut through a wide variety of materials. Unlike other cutting methods that generate heat, abrasive water jet cutting maintains a non-thermal approach, preventing any heat-affected zones on the material surface. This allows for clean, smooth edges without compromising material integrity, making it an ideal choice for projects that require precise cuts with minimal post-processing.
By adjusting the water pressure and abrasive feed, abrasive water jet cutting can be tailored to handle different materials and thicknesses, from soft rubbers and plastics to hard metals and ceramics. This flexibility, combined with its ability to cut complex shapes, has made abrasive water jet cutting a valuable tool in various industries.
How the Abrasive Water Jet Cutting Process Works
Abrasive water jet cutting operates through a carefully controlled sequence of steps, utilizing high-pressure water and abrasive particles to produce clean, precise cuts:
- High-Pressure Water Stream: A high-pressure pump generates a stream of water, often reaching between 4,000 and 6,000 bar. This intense pressure propels the water through an orifice in the cutting head.
- Abrasive Mixing: Once the water stream is created, garnet blasting media or another abrasive is introduced into the stream through an abrasive inlet, combining with the water to form a powerful cutting tool.
- Focusing Tube and Cutting Head: The abrasive-laden water jet is directed through a tungsten-carbide focusing tube, where it is concentrated into a high-speed stream. This high-velocity jet is capable of cutting through thick materials with precision, shaping everything from metals to composites.
- Adjustable Cutting Parameters: By modifying parameters like water pressure and abrasive flow rate, operators can optimize the process for specific material types and thicknesses, achieving the desired cut quality and efficiency.
Polycut Waterjet Abrasive: Precision and Efficiency
Polycut waterjet abrasive is an advanced option that provides both sharp cutting edges and optimal flow rates, ideal for achieving high precision in intricate cuts. Its consistency ensures smooth operation and enhanced speed, making it a reliable choice for projects demanding accuracy.
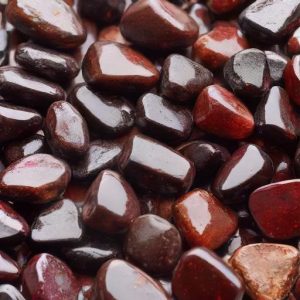
Advantages of Abrasive Water Jet Cutting
Abrasive water jet cutting offers a range of benefits that make it a preferred choice across industries:
- Heat-Free Cutting: As a non-thermal process, water jet cutting avoids creating heat-affected zones, preserving the material’s properties and integrity.
- Material Versatility: This method can cut nearly any material, from metals and composites to ceramics and rubber, making it suitable for diverse industrial applications.
- Precision and Flexibility: With high cutting accuracy, water jet systems can produce intricate shapes and designs, reducing the need for secondary finishing processes.
- Environmentally Friendly: Abrasive water jet cutting uses natural abrasives like garnet, which can be recycled and repurposed, making it an eco-friendly option.
Applications of Abrasive Water Jet Cutting in Industry
Abrasive water jet cutting is widely used across industries that require high precision and versatility. In the aerospace sector, it’s ideal for cutting composites, titanium, and other materials used in aircraft manufacturing, where maintaining material integrity is critical. Automotive manufacturers benefit from water jet cutting’s ability to handle complex shapes and various materials, from metals to synthetic materials.
This cutting method is also valuable in construction and manufacturing, where it provides a clean, heat-free cutting solution for thick materials like stone, glass, and ceramics. Its flexibility in handling a variety of materials and thicknesses makes abrasive water jet cutting a go-to method for industries demanding both precision and adaptability.
Selecting the Right Abrasive for Your Project
Achieving the best results in water jet cutting starts with choosing the right abrasive. Garnet remains the preferred choice for its unmatched balance of durability and cutting power, allowing you to deliver high-quality cuts while protecting your equipment. By investing in a high-purity, uniform abrasive, you can maximize productivity and precision, ensuring each cut meets your standards with minimal downtime. NT Ruddock provides premium garnet abrasives tailored to meet the needs of your specific project, helping you enhance efficiency, improve cut quality, and extend equipment lifespan. Discover the difference our top-grade abrasives can make in your water jet cutting operations.